How Much Does It Cost To Start A Mini Cement Manufacturing Plant?
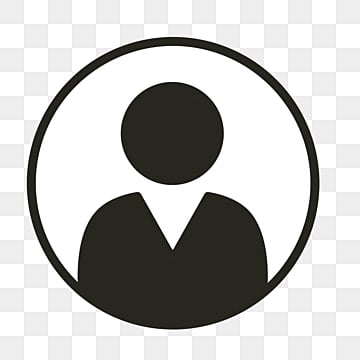
Yunus Khan Tunvar
Yunus Khan Tunvar is the CEO of the Cement Division at NandT Engitech Pvt. Ltd. With extensive experience in the industry, he leads his team with a focus on innovation and quality. Under his guidance, the division has seen significant growth and success, setting new standards in the cement sector.
Build Something People Want
Let's talk about your engineering needs to find the best solutions.
Submit Your Business Inquiry
Are you interested in learning more about our technologies? Feel free to contact us right away to discuss your project.